Å løse problemet med prosesseffektivitet har to positive effekter.
Først av alt, å introdusere spiralmatet prosessering i prosessen – som vi har sett – gir råvarebesparelser som til og med kan være i overkant av tjue prosent for samme mengde produkt, og det betyr positive marginer og kontantstrøm som er umiddelbart tilgjengelig til selskapet.
Dette kan variere avhengig av sektor og bruk: uansett er det materiell som gründeren og selskapet ikke lenger trenger å kjøpe, og avfallet trenger heller ikke å håndteres eller deponeres.
Hele prosessen er mye mer lønnsom og det positive resultatet kan sees umiddelbart på resultatregnskapet.
Videre, ved å kjøpe mindre råstoff, gjør selskapet automatisk prosessen mer bærekraftig, fordi den råvaren ikke lenger trenger å produseres nedstrøms!
Energieffektivitet er et annet viktig element i kostnadene for hver produksjonssyklus.
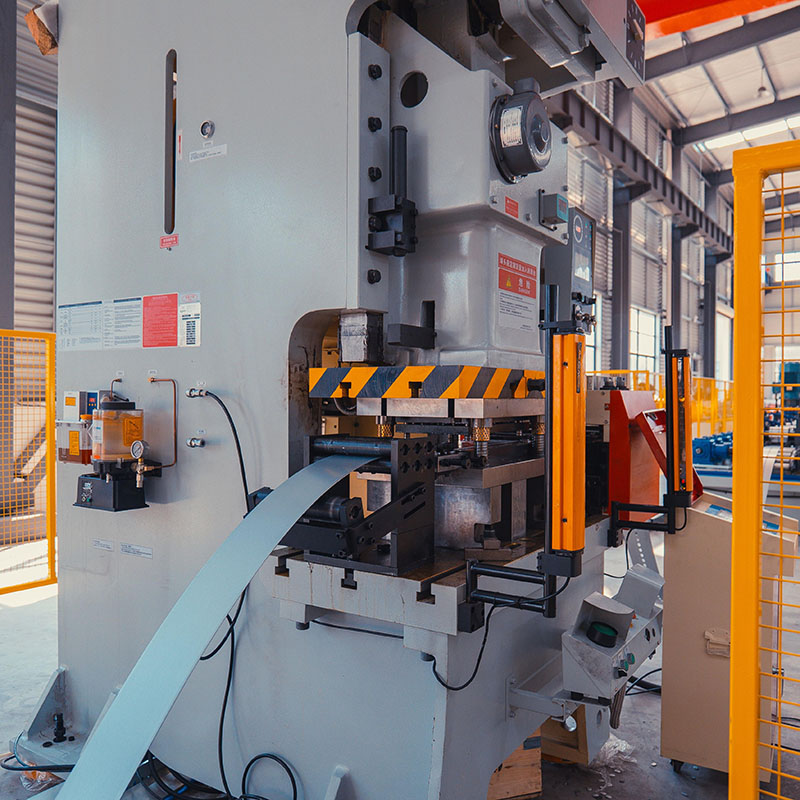
I et moderne produksjonssystem er forbruket av en rulleformingsmaskin relativt lavt.Takket være Combi-systemet kan linjer utstyres med flere små motorer drevet av omformere (i stedet for én, stor spesialmotor).
Energien som brukes er nøyaktig den som kreves av formingsprosessen, pluss eventuell friksjon i transmisjonsdelene.
Tidligere var et stort problem med hurtigskjæremaskiner energien som ble spredt via bremsemotstandene.Faktisk akselererte og bremset klippeenheten kontinuerlig, med et stort energiforbruk.
I dag, takket være moderne kretser, kan vi akkumulere energi under bremsing og bruke den i rulleformingsprosessen og i den påfølgende akselerasjonssyklusen, gjenvinne mye av den og gjøre den tilgjengelig for systemet og andre prosesser.
Videre styres nesten alle elektriske bevegelser av digitale omformere: sammenlignet med en tradisjonell løsning kan energigjenvinningen utgjøre opptil 47 prosent!
Et annet problem angående energibalansen til en maskin er tilstedeværelsen av hydrauliske aktuatorer.
Hydraulikk utfører fortsatt en svært viktig funksjon i maskiner: det er for tiden ingen servoelektriske aktuatorer som er i stand til å generere så mye kraft på så liten plass.
Når det gjelder spolematede stansemaskiner, brukte vi de første årene kun hydrauliske sylindre som aktuatorer for stansene.
Maskinene og kundenes behov fortsatte å vokse, og det samme gjorde størrelsen på de hydrauliske kraftenhetene som ble brukt på maskiner.
Hydrauliske kraftenheter bringer olje under trykk og distribuerer den til hele linjen, med påfølgende fall i trykknivået.
Oljen varmes da opp og mye energi går til spille.
I 2012 introduserte vi den første servoelektriske spolematede stansemaskinen på markedet.
På denne maskinen byttet vi ut de mange hydrauliske aktuatorene med et enkelt elektrisk hode, administrert av en børsteløs motor, som utviklet opp til 30 tonn.
Denne løsningen gjorde at energien som kreves av motoren alltid kun var den som kreves for å kutte materialet.
Disse servoelektriske maskinene bruker også 73 % mindre enn tilsvarende hydrauliske versjoner og gir også andre fordeler.
Faktisk må hydraulikkolje skiftes omtrent hver 2000. time;ved lekkasjer eller ødelagte rør tar det lang tid å rydde opp og fylle på, for ikke å snakke om vedlikeholdskostnader og kontroller knyttet til et hydraulisk system.
Den servoelektriske løsningen krever imidlertid bare etterfylling av den lille smøremiddeltanken, og maskinen kan også kontrolleres fullstendig, selv eksternt, av en operatør og en servicetekniker.
I tillegg tilbyr servoelektriske løsninger omtrent 22 % raskere behandlingstider sammenlignet med hydraulisk teknologi. Hydraulisk teknologi kan ennå ikke elimineres helt fra prosessene, men vår forskning og utvikling er absolutt rettet mot den stadig mer utbredte bruken av servoelektriske løsninger på grunn av mange fordeler de gir.
Innleggstid: 23. mars 2022